MIM
Possible to create 3D complex shapes
on the order of millimeters
on the order of millimeters
We are confident about micro-molding skills and create a future with micro parts
MIM (Metal Injection Molding) is a metalworking process in which finely powdered metal is mixed with binder material to create a "feedstock" that is then shaped and solidified using injection molding.
From very early on, we focused on Metal Injection Molding and conducted research and development without relying on technology imports from the U.S. In 1991, we acquired a patent in the U.S. and accomplished a base of Metal Injection Molding.
At each base factory, we handle thin-wall and complex shape products through an integrated system from mold manufacturing to raw material production.
From very early on, we focused on Metal Injection Molding and conducted research and development without relying on technology imports from the U.S. In 1991, we acquired a patent in the U.S. and accomplished a base of Metal Injection Molding.
At each base factory, we handle thin-wall and complex shape products through an integrated system from mold manufacturing to raw material production.
CASTEM Color
Examples of Proposals
01
Elimination of Machining
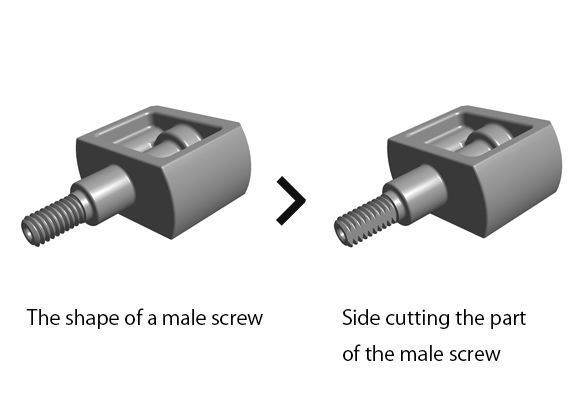
02
Quality Improvement
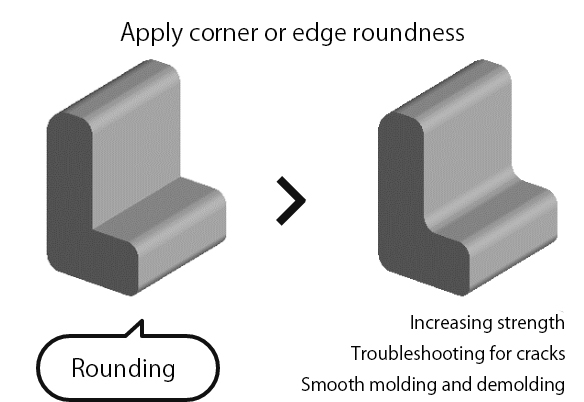
03
Reduction in Thickness and Weight
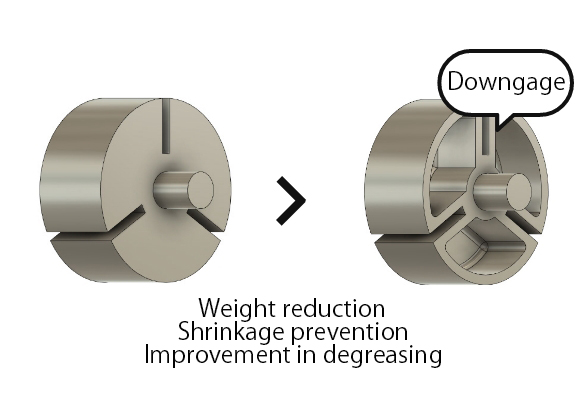
Manufacturing Process
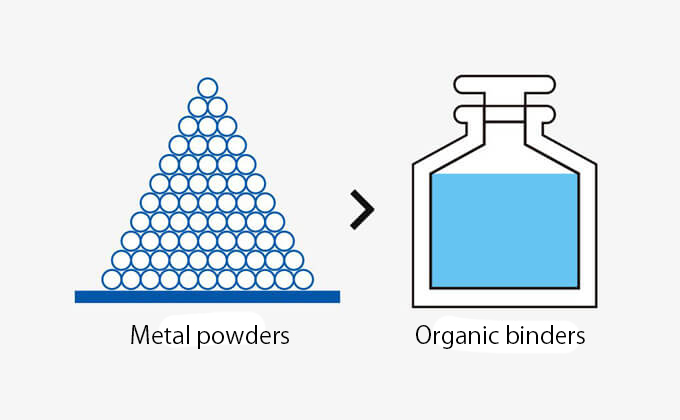
01. Feedstock Preparation
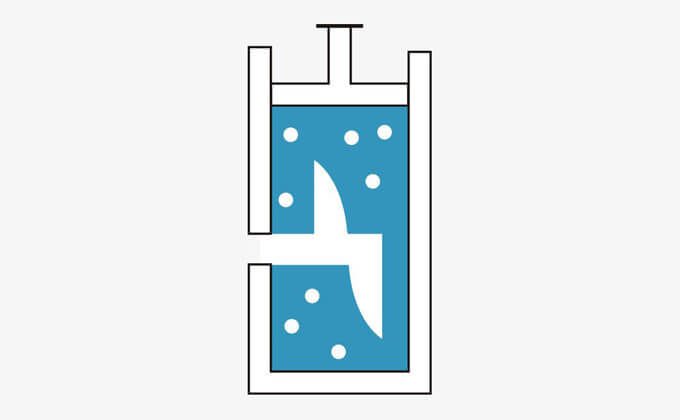
02. Mixing
Combine metal powders with binders
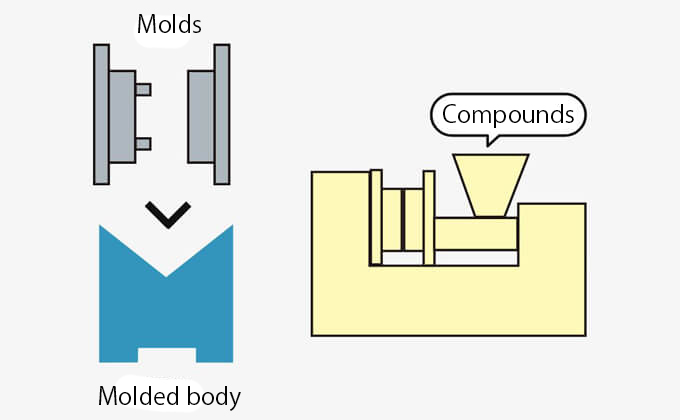
03. Injection Molding
Create molded body by injecting heated compounds into the inside of molds
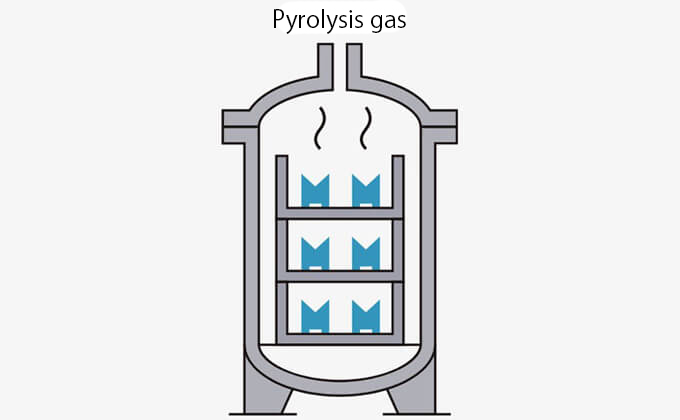
04. Thermal debinding
Remove organic binder from the molded body
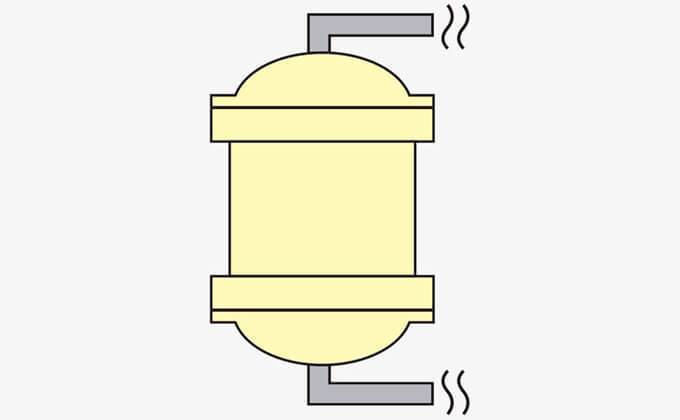
05. Sintering
Create high-density sintered body at a high temperature
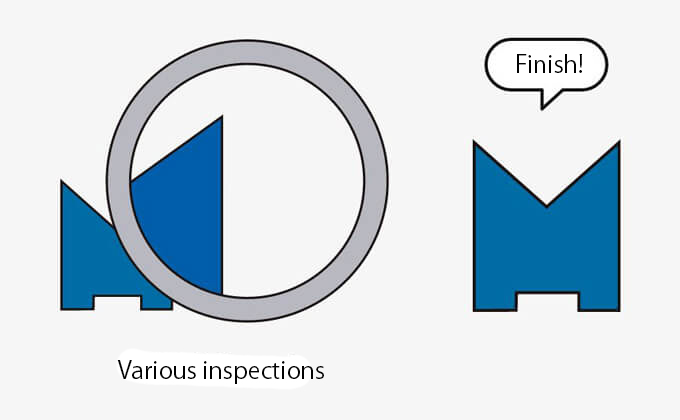
06. Inspection
Inspect the quality according to various quality standards
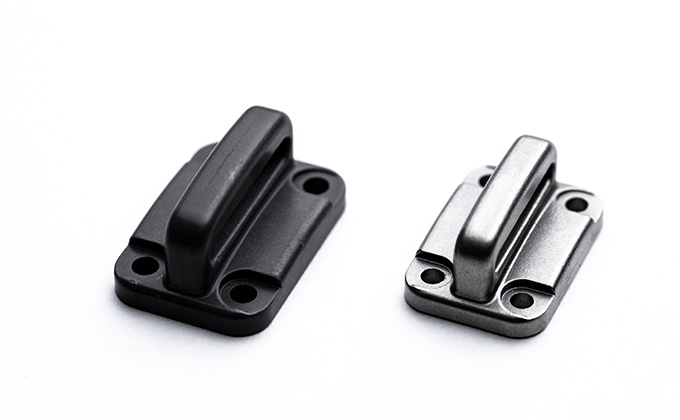
Injection Molded Body and MIM Sintered Body
The one on the left is the molded body, and the one on the right is sintered body. It is possible to produce highly precise products because the shrinkage is approximately equal.
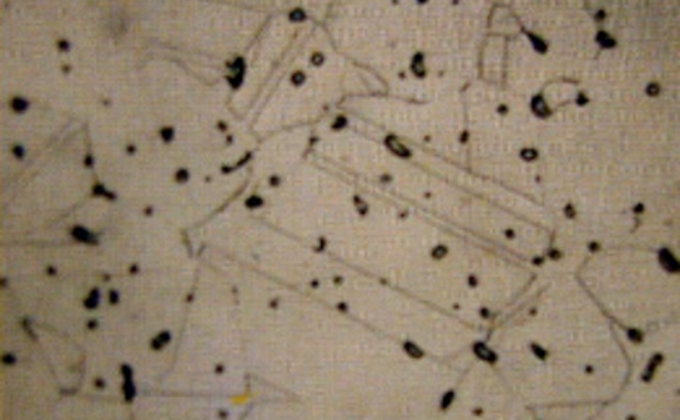
MIM
The body made by MIM has excellent mechanical strength properties because its density reaches over 95% and its vacancies are spherical and independent.
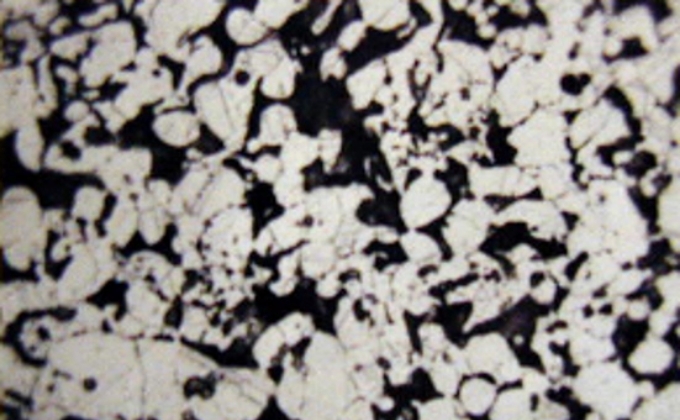
Conventional Sintering
The body made by standard sintering has poor mechanical strength properties because its density reaches only 88% and its vacancies exist along the grain boundary irregularly.
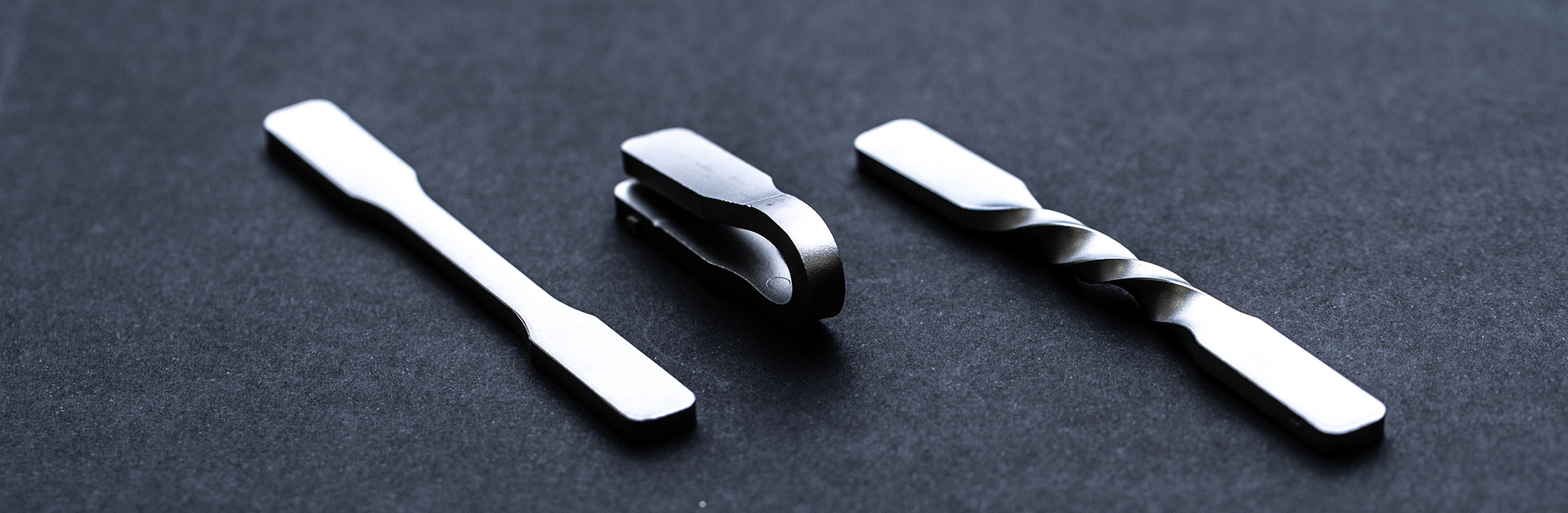
It indicates properties similar to that of molten material such as torsion and spring. (The products in the photo are made of SUS304)
Catalog Download
Materials
Classifications | Materials |
---|---|
Chromium molybdenum steel | SCM415 |
Nickel chromium-molybdenum steel | SNCM439 |
Tool steel | SKD11 |
High-speed steel | SKH57 |
Stainless alloy (Austenitic, Martensitic, Precipitation hardening) | SUS304L, SUS316L, SUS420J2, SUS630 (17-4PH) |
Heat-resistant steel | HK-30 |
Special steel | Kovar, Permalloy, Co-Cr-Mo alloy, Fe-3%Si |
Cemented carbide | WC-10%Co |
Magnetic and low thermal expansion alloy | Fe-42%Ni |
Titanium | pure titanium, 6AL4VTi |
Tolerance Chart (mm)
Dimension | Unspecified tolerance |
---|---|
0 - 5 | ±0.10 |
5 - 10 | ±0.10 |
10 - 20 | ±0.15 |
20 - 50 | ±0.20 |
50 - | ±1.0% |
Angular tolerance | ±1.0° |
Size Guides
Minimum size | approximately a few millimeters |
---|---|
Maximum size | approximately 10cm |
Minimum weight | approximately 1g (minimum thickness: 0.2mm – 5mm) |
Maximum weight | approximately 100g |